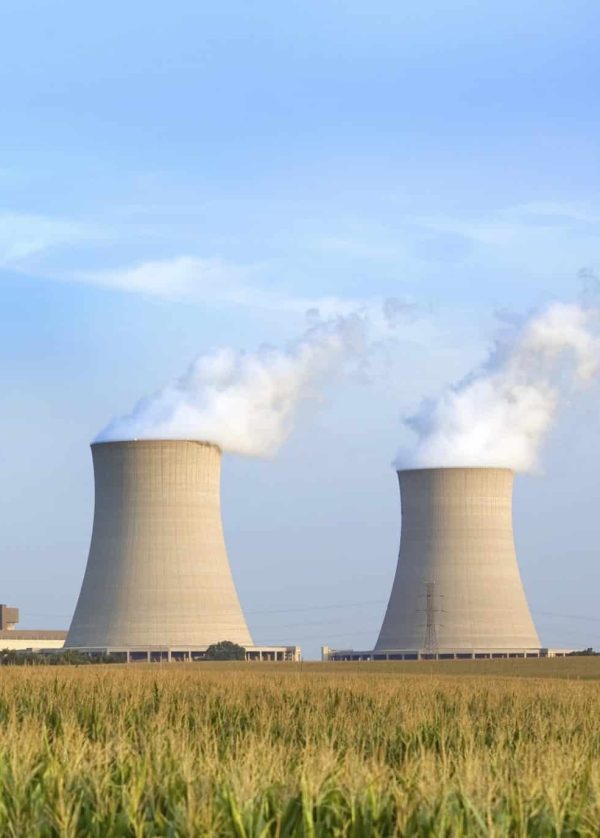
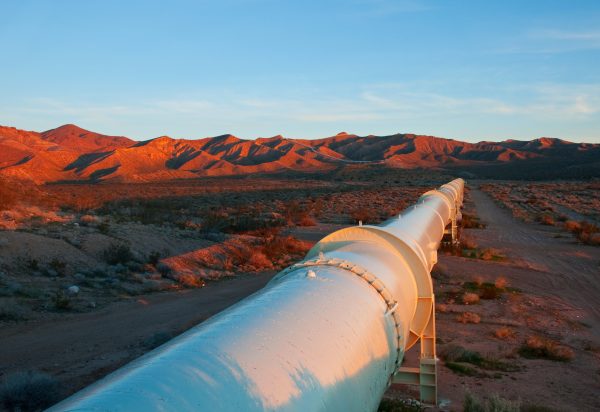
Our Specialties
Featured Product
-
DA 99
Heavy-duty servo actuator for spot welding and other industrial applicationsThe DA 99 series Roller Screw Servo Actuator is a time-proven solution for welding guns. The powerful 10-pole synchronous motor and in-house designs provide high performance and protection against water and welding sludge.
Join Our Team
-
FIELD SERVICES
-
QUALITY & HSE
-
ENGINEERING
-
CORPORATE BUSINESS
-
MANUFACTURING & PRODUCTION
-
Principle Markets
Established
1990
Quality Management System
ISO 9001:2015
Let's Work Together
-